Vibration measurement of a paper machine winder
Case Overview
Our customer was a Finnish hardware manufacturer who manufactured winders and made selling internationally. one of its end users in China reported abnormally high vibration levels in the device our customer sold. Our customer wanted to find out the matter quickly. Nome experts carried out measurements and vibration analysis at a Chinese paper mill. Things were handled together with Nome, the manufacturer and the user of the device. The operation of the unit and the production of the plant could be continued without long service shutdowns.
Customer
A Finnish winder manufacturer with operations around the world in 2007.
Challenges
The client had shipped a paper machine winder from Finland to a Chinese paper mill. However, The machine did not pass the inspection by the end user due to abnormally high vibrations. The end user rejected to sign the receiving document since they perceived it did not match the quality requirements. The client sent Nome experts to the end user’s facility to check the condition in order to make an informed decision to remedy this issue.
Solution
Dynamics of winders is a complex problem, the challenges came from constant changes in speeds, masses and control parameters. Nome’s professionals’ expertise has covered many winders, making a variety of grades of paper, hence have a range of problems’ solutions. After the travel arrangements, Nome specialist flew to China to Perform an inspection of the machine and report any issues in a timely manner.
Machine condition analysis
Vibratory measurements were performed on the winder and the machine was monitored for several days. The characteristics of the winders sometimes included relatively strong vibrations on some paper grades. To identify the source of the winder vibration, the frequency of the vibrations were related to rotation speeds, cutter type, paper quality and driving parameters. Based on the measurements made, the winder was fine. The occasional vibrations (moderate frequency) caused a relatively strong sound. However, this did not affect the operation of the winder.
Result
Nome issued a detailed inspection report, showing the condition and quality of the product and any issues found. Based on the report, the end user accepted the product. Both sides were well satisfied. On one hand, Nome’s inspection assured the end user that the winder would perform adequately its intended function and can be used safely. On the other hand, the inspection provided valuable information to the client about the vibration of the device for further research and development.
Equipment
- Multichannel measuring equipment
- Acceleration sensors
- Tacho sensors
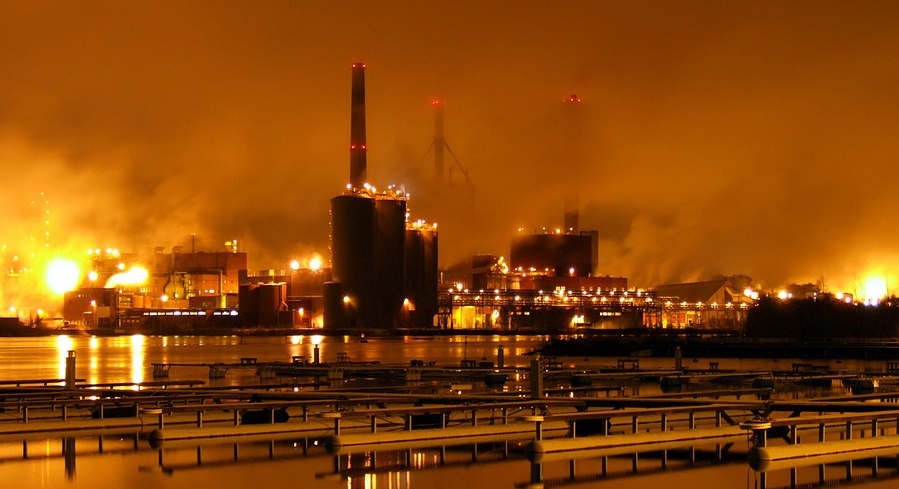